Services
PROTECTING LIVES,
DRIVING EFFICIENCY,
EMPOWERING SUCCESS
Helping make change a success at every step of the cold chain journey. From solution qualification, current to future state process implementation, parcel and bulk preparation to inventory or fleet management. Through voice of customer and service innovation, we are building the future of cold chain servicing that offers a level of accuracy and traceability unmatched in the industry to continually improve patients' lives worldwide.
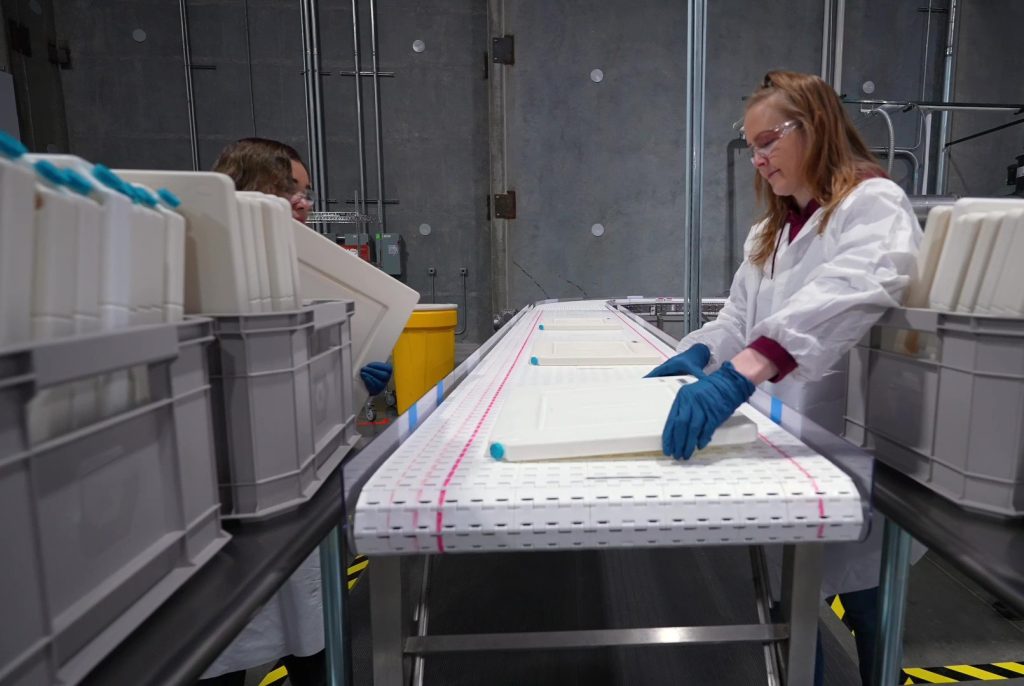
Why choose Peli BioThermal?
- Trusted AvailabilityReduce costly inventory, storage and conditioning space by switching to a Peli managed, lease or rental program making room for payload and growth
- No Brainer QualificationTested to the highest profile and probing standard provides peace of mind payload and patient protection
- Successful ImplementationReach go-live without delay by working together with our team to adapt our flexible product and service portfolio to each unique business and program need
- Perfect PreparationMitigate conditioning and assembly errors entrusting our expert service teams worldwide to prepare your solution correctly and consistently.
- True ReusabilityLower CO2 emissions and landfill usage by switching to a lighter, smaller and highly reusable solution built to last between 5-10 years at high turn rates.
Trusted Availability
Supply chain issues are inevitable yet create inventory pressure to ensure stock is available. This results in costly excess safety stock taking the space of revenue generating product. Outsourcing the management and preparation of stock to Peli BioThermal leaves room to increase site capacity, broaden patient reach and reuse for our planet.
Peli Managed Inventory
Lease
Rental
Rental Parcel
Credo Cube
CredoGO
CoolGuard Advance
CoolGuard PCM
Bulk
Credo Vault
Credo Cargo
Credo Xtreme
CoolPall Flex
Define the right solution portfolio combining single use (managed) and reusable (lease) products to handle hard to reach and easy to return locations. All re-stocked, refurbished and ready to the next use by our Peli BioThermal service centers.
Hover over the diagram above
No Brainer Qualification
Our clients trust Peli BioThermal to qualify solutions to the highest quality to mitigate real-world product failures. All three of our EMEA and US based laboratories are accredited to ISO17025, follow standardized thermal qualification processes and offer large testing capacity with over 30 chambers worldwide.
Solutions suited to domestic, cross-border and international lanes to strict and lenient storage requirements.
Fully mapped probing protocol using placebo payload to simulate real world conditions to worst cases scenarios.
Our experienced engineering team can cover everything from design feasibility to operational qualification to drop testing.
Successful Implementation
Current solutions, future goals and stakeholder needs vary from business to business. Peli BioThermal specializes in adapting our solution portfolio to select the best suited product, service and software package to help reach go-live with confidence and trust in our preparation.
Dedicated account, product and project team to define the current solution and business need
Complete implementation support from agreement execution to program dry runs
Perfect Preparation
Keeping highly skilled staff can be challenging. Temporary staff are often the only choice resulting in conditioning and preparation errors putting valuable pharmaceuticals and sensitive life-saving treatments are risk of thermal excursion and patients without treatment. Peli BioThermal take the worry and pressure away preparing each solution to optimal conditioning processes all traced against our global and harmonized quality management system
RE-STOCK
& REUSE
& REUSE
Maintain solution availability based on forecast data
FLEET
MANAGEMENT
MANAGEMENT
INVENTORY
MANAGEMENT
MANAGEMENT
Store, track expiry and usage to ensure solution availability
when the unpredictable occurs
CONDITIONING
& ASSEMBLY
& ASSEMBLY
Traceable and optimal conditioning and expert assembly processes to maximize protection even when delivered ready to load
PARCEL & BULK
REPAIR
REPAIR
Solutions are repaired back to manufacturing specification, extend lifespan and utilization whilst reducing waste
PARCEL & BULK
REFURBISHMENT
REFURBISHMENT
All reusable solutions are refurbished back to manufacturing specification, ensuring each shipment is as secure as the last
RETURN
MANAGEMENT
MANAGEMENT
Peli BioThermal will work with the logistics provider and customer to efficiently return solutions back to be used again.
DELIVERED
READY TO
LOAD
READY TO
LOAD
True Reusability
Trust in Peli BioThermal to provide reusable solutions built for consistent use over years in the field, with minor repair, driving down long-term packaging and freight costs reusing high quality materials that are light and efficient to ship, whilst maintaining trusted end to end thermal protection.
Year 5 to 10
Our reusable TIC(TM) coolants are designed to last 10 years maximizing solution lifespan
Year 1
Year 5
Our reusable parcels solutions are built to last 5 years or more in the field significantly minimizing landfill usage
Year 2
Year 4
Year 3